Fast, faultless and better for the environment: The BMW Individual factory at the Dingolfing plant uses artificial intelligence to calculate and cut leather. With the aid of the Automatic Surface Inspection system, leather surfaces for BMW and BMW M vehicle interiors can be better calculated, used more effectively and tailored more precisely. The process means a significant reduction in waste and about 15 percent less leather consumption, conserving resources and lowering CO2 emissions.
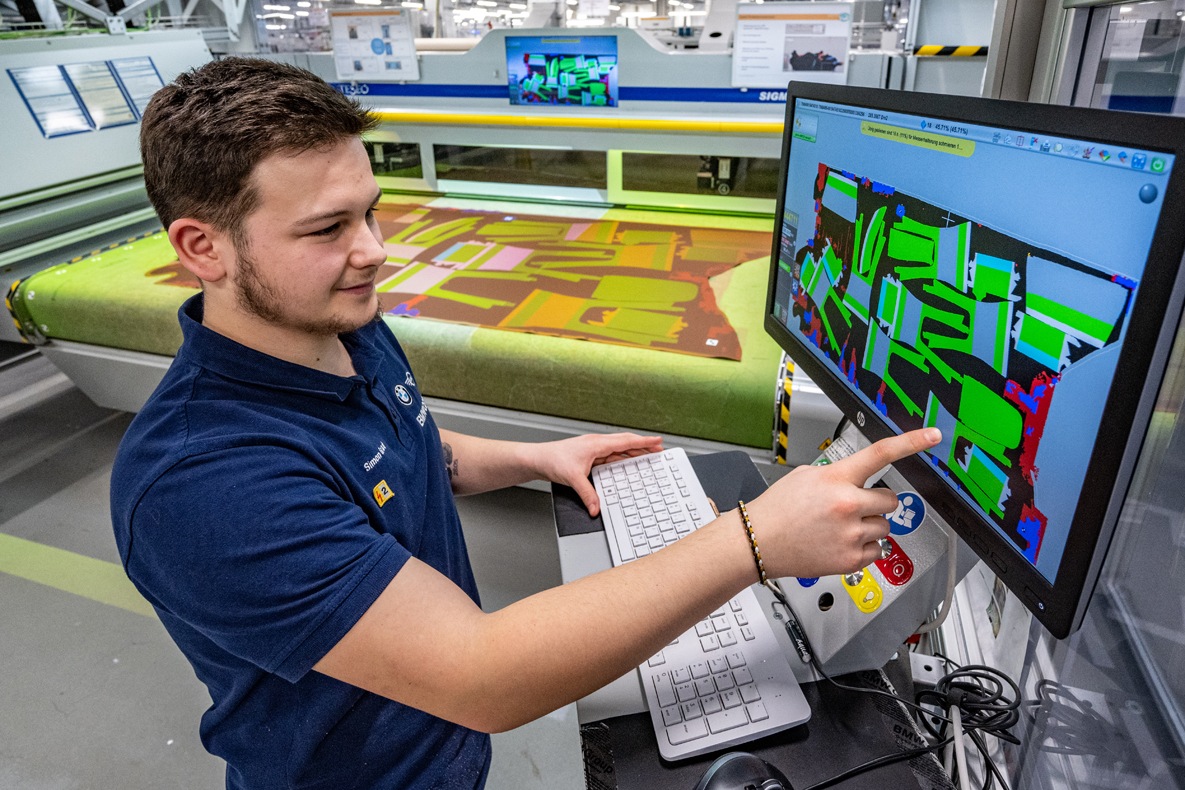
The screen shows intricately interlocking patterns which have been calculated by the computer.
HOW IT WORKS.
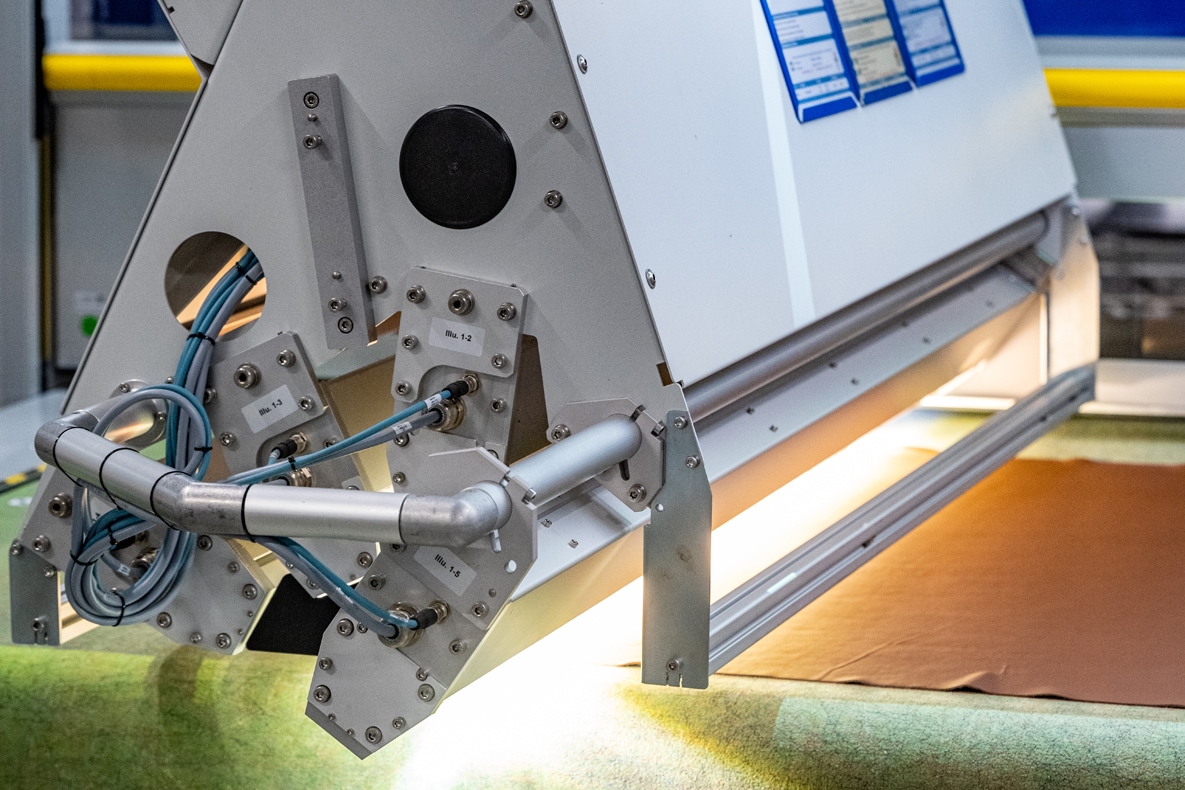
HOW IT WORKS.
The large scanner hums quietly as it moves over the leather. Its cameras register every unevenness, every bulge. The dyed material lying on the cutting table is destined to become seat covers for a BMW M3. On the screen beside the scanner appears a depiction of the surface of the leather, marked with dots, lines, coloured markings and numbers. “Here we see which parts of the leather can be used and which are scrap,” explains Marco Loistl, Head of Production and Maintenance at the BMW Individual factory in the Dingolfing plant. The screen shows interlocking patterns placed over the whole area in seconds by the computer. “And the programme also calculates the best positioning for the cutting parts,” says Loistl.
“EVERY WASTED PIECE HURTS.”
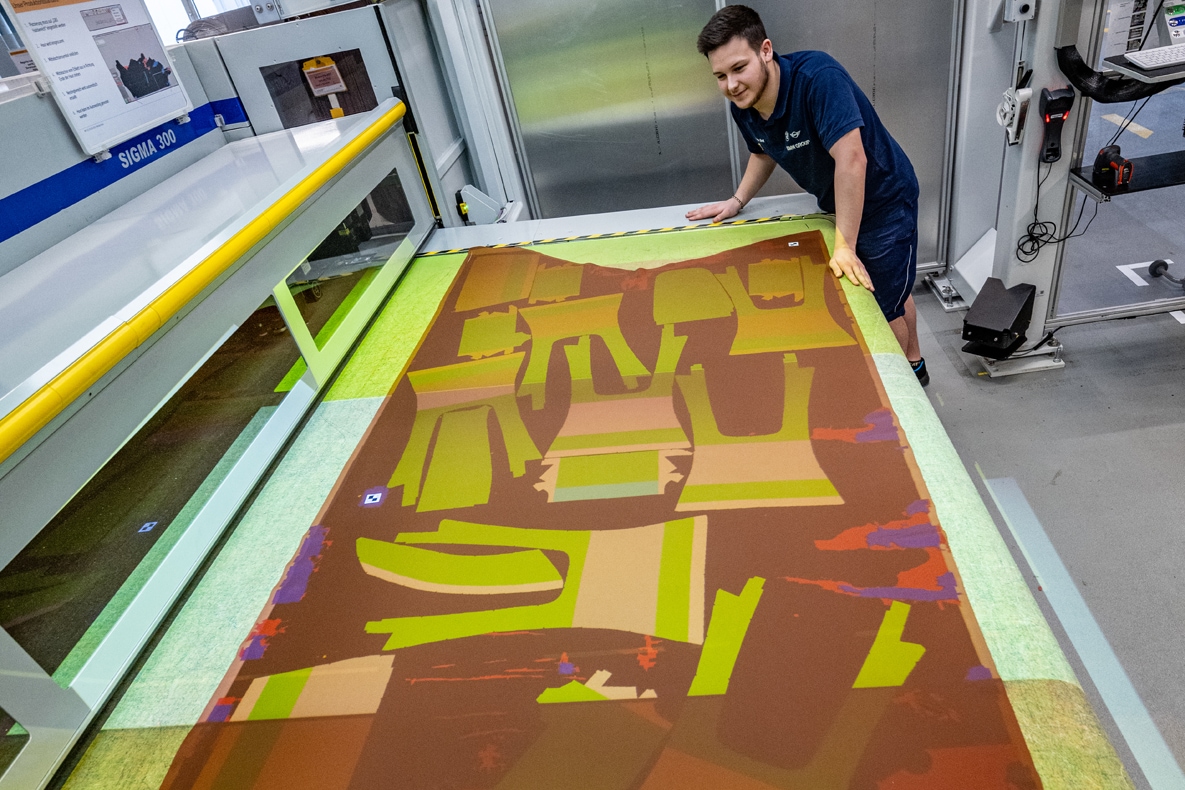
“EVERY WASTED PIECE HURTS.”
The Individual factory at the BMW Group’s Dingolfing plant makes interior components for BMW vehicles with special equipment – for example dashboards with leather fittings for BMW M automobiles from the 3, 4, 5 and 7 series, along with the iX M60. It is a small field, with around 200 people employed in the production. “When you work with a living material like leather, every bit of waste, every unusable scrap of leather hurts,” says Loistl. “And even the best quality leather has tiny scars. If such natural features are too marked, then that piece cannot be used.”
NATURE MAKES CUTTING DIFFICULT.
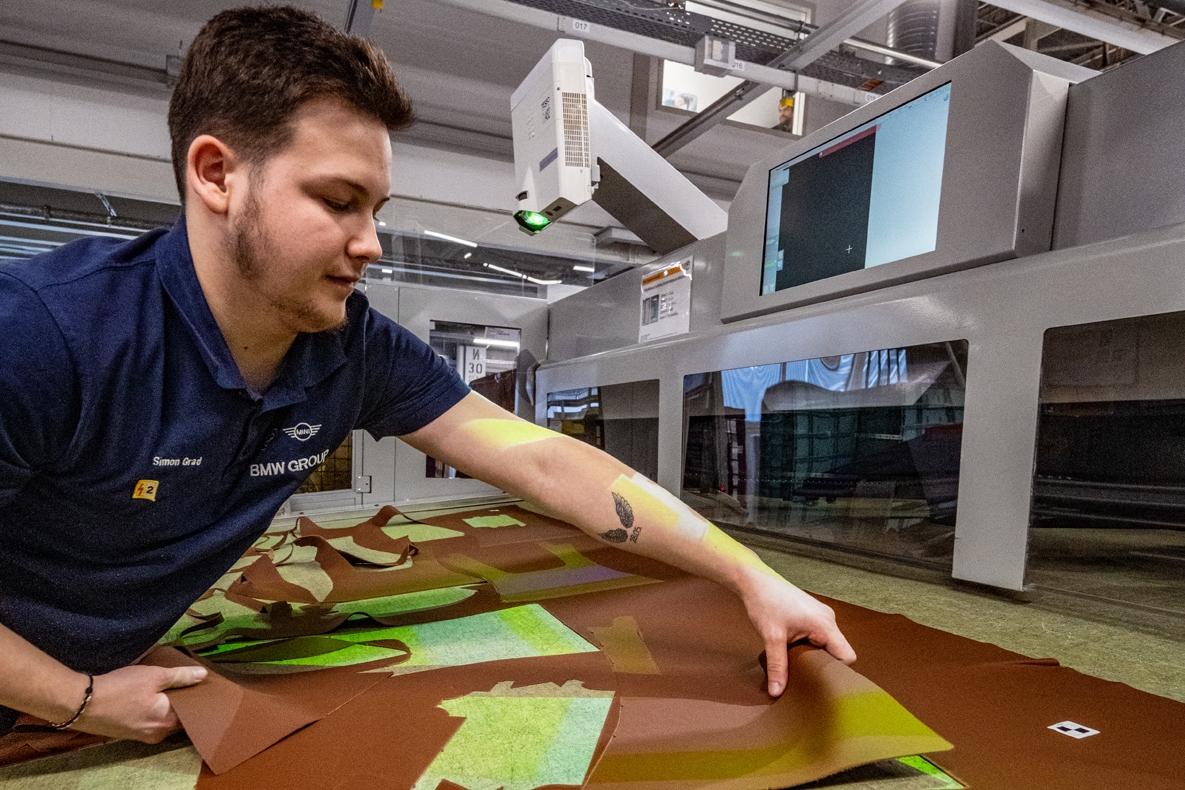
NATURE MAKES CUTTING DIFFICULT.
Depending on the area of use, about three quarters of the leather flatware, as tanned smooth leather is called, can be used in the vehicle. The reason: an animal skin is not a simple oblong, but has a natural shape which makes cutting more difficult. And then there are the natural features.
Next door, at the cutting table a robotic arm armed with an oscillating blade begins moving, a few millimetres above the skin. With millimetre precision, it tailors the separate parts of the leather. The cut and finished parts then go to the sewing room.
SEARCHING FOR EVERY MOSQUITO BITE.
To maximize the usable parts and avoid contamination of the leather, back in 2018 the BMW Individual factory in the Dingolfing switched from marking the leather by hand with chalk to digital marking. Nevertheless, the staff still have to work with extreme care when inspecting the skins for the tiniest fault, like mosquito bites. This is not only strenuous on the eyes, the specialists are also constantly faced with questions: Is the feature still acceptable or a fault? If it can still be used: For which area is the leather suitable, how will the location be classified?
“You can’t do this work very long at a stretch,” says Marco Loistl. “That’s why we started feeding recognition software with the knowledge of our best employees.” Similar software was already in use in the glass manufacture to spot air pockets and bubbles. Adapting it for the leather inspection was an obvious option. In 2021, the programme took over from the staff and now the leather is inspected automatically and divided into classes.
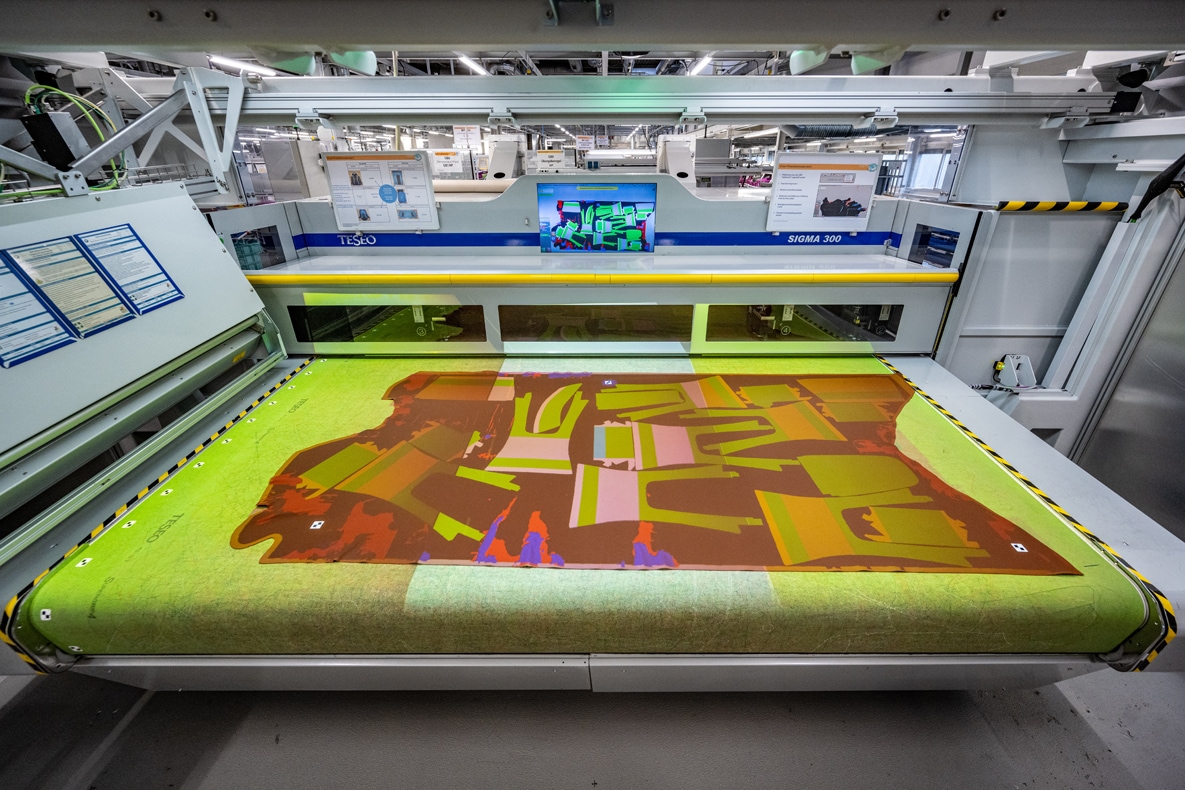
Cutting leather is a bit like baking biscuits. You try to place as many cut portions as possible alongside each other so that you waste as little material as possible.
DIGITAL TRIAD.
Developing the system was expensive and time-consuming, but the results show that it was the right move: reduced used of resources, lower costs in purchasing and a better CO2 balance. From automatic surface inspection to a completely digitalized process was thus a logical step. Since early 2022, digital inspection and classification of the leather, along with nesting and cutting, have been combined in a single system. During nesting, the programme digitally positions the leather sections for cutting in the available space and they are then tailored by the machine in the cutting process.
The results of the new process are excellent: With the same amount of leather-covered interior parts, leather consumption at the Dingolfing plant has fallen by about 15 percent. The number of wrongly cut or faulty pieces of leather has fallen by as much as 75 percent. Digitalisation thus helps to make the process more effective and reduce costs. At the same time, it simplifies the work and protects the environment.